Kickstarting a well with damaged screens
North Sea, May 2018
North Sea, May 2018
Challenge
A major Norwegian oil and gas producer experienced a screen collapse in one of their highest producing wells. This caused a significant volume of sand to enter the wellbore, which then entered the production facility itself. The well was immediately shut in due to the operator’s topside sand handling capacity. A wireline operation was conducted to confirm the collapse but was held up at a shallow depth of 1 575m. It was then assumed that the well was almost filled with solids.
The well was scheduled for a plug and abandonment (P&A) campaign followed by the drilling of a side-step to regain production. To facilitate the P&A operation, the wellbore had to be cleaned down to the appropriate depth to allow for setting of barrier plugs. A coiled tubing (CT) operation, estimated to cost $3.5m, would be a typical solution for these types of cleanout purposes. However, a DualFlow unit was already installed and in operation, connected to more than 20 wells via the test manifold in the production system, as part of a continuous production solution. As a result, the client asked us to evaluate the well before commencing CT.
The well was scheduled for a plug and abandonment (P&A) campaign followed by the drilling of a side-step to regain production. To facilitate the P&A operation, the wellbore had to be cleaned down to the appropriate depth to allow for setting of barrier plugs. A coiled tubing (CT) operation, estimated to cost $3.5m, would be a typical solution for these types of cleanout purposes. However, a DualFlow unit was already installed and in operation, connected to more than 20 wells via the test manifold in the production system, as part of a continuous production solution. As a result, the client asked us to evaluate the well before commencing CT.
Solution
After evaluation it was decided to attempt to kick-start the well using a 5K psi DualFlow desander. This would dramatically remove sand at the well’s surface. No detrimental impact was identified during the evaluation of a kick-start attempt on the well and the initial production recovery was undertaken. If successful, the cost and associated emissions of additional personnel on board (POB) and the logistic impact would also be eliminated.
Results
The well was kick-started, and the sand causing the blockage was removed. During the initial production recovery stage, the total production earnings from recovered oil was $1.4m. The well was returned to continuous production with the indication of high oil production potential.
Having returned the wells to full production and removed the need for CT, the client saved an estimated $3.5m of CT costs. When this is brought together with the $1.4m revenue generated in the recovery stage is equated to a total planned operation difference of $4.9m.
The well continues to be produced through the 5K DualFlow, providing an average oil production of ~560Sm³/day. The wellbore is maintained at surface with a separation efficiency of >99%, and since all sand is continuously transported out of the wellbore, integrity is retained. Total solids removed (YTD) of 7 817kg.
Having returned the wells to full production and removed the need for CT, the client saved an estimated $3.5m of CT costs. When this is brought together with the $1.4m revenue generated in the recovery stage is equated to a total planned operation difference of $4.9m.
The well continues to be produced through the 5K DualFlow, providing an average oil production of ~560Sm³/day. The wellbore is maintained at surface with a separation efficiency of >99%, and since all sand is continuously transported out of the wellbore, integrity is retained. Total solids removed (YTD) of 7 817kg.
Outcomes
Production was recovered without CT, restoring an average oil production of 560Sm³/day
During the operation, achieving a higher sand free oil production, gave a direct profit of $0.23m/day
$1.4m revenue generated in the recovery stage equated to a total planned operation difference of $4.9m.
The well was maintained at the surface with a separation efficiency of >99%.
Total solids removed (YTD) were 7,817kgs.
All sand was continuously transported out of the wellbore ensuring enhanced recovery
Estimates of a conservative 250 production days for a full year, gives a total earning due to the 5K DualFlow production enhancement system of $58m
During the operation, achieving a higher sand free oil production, gave a direct profit of $0.23m/day
$1.4m revenue generated in the recovery stage equated to a total planned operation difference of $4.9m.
The well was maintained at the surface with a separation efficiency of >99%.
Total solids removed (YTD) were 7,817kgs.
All sand was continuously transported out of the wellbore ensuring enhanced recovery
Estimates of a conservative 250 production days for a full year, gives a total earning due to the 5K DualFlow production enhancement system of $58m
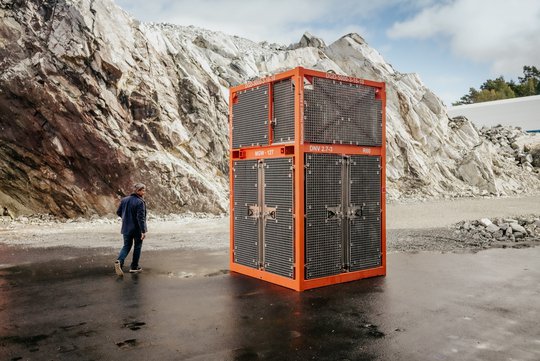
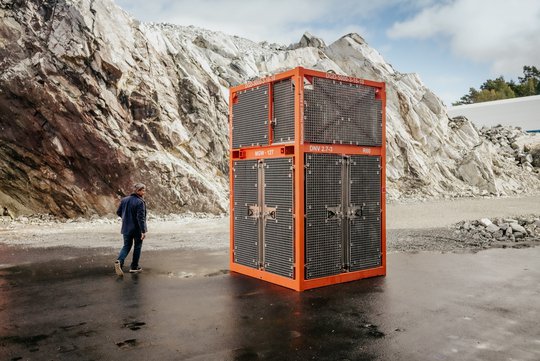