Insights: The key differentiators of a smart desander
The key difference between basic desanders and a smart desander is that the latter has been designed and engineered with their intended use in mind- optimizing production.
There are three main types of desanders on the market:
• Basic multiple liner desanders – these are typically associated with separating oil from water
• Desanders without a liner – made for well testing.
• Single liner desanders – a smart desander that is designed for production optimization, while also handling solids
It is important to note that not all smart desanders are created equally. For the purpose of this article, we will refer to the DualFlow 5K PSI. Qualified by DNV with an efficiency rating of 99.8% for topside separation down to 20 microns and up to 10,000 microns. The DualFlow 5K PSI is a market leader in solids management and is particularly adept at multiphase solids separation. This means they are designed for optimizing production on both gas and oil producing wells and, at the same time, handling the solids in return with high efficiency.
There are many differentiators between regular desanders and smart desanders; this article aims to outline the key differentiators from a design and engineering perspective.
There are three main types of desanders on the market:
• Basic multiple liner desanders – these are typically associated with separating oil from water
• Desanders without a liner – made for well testing.
• Single liner desanders – a smart desander that is designed for production optimization, while also handling solids
It is important to note that not all smart desanders are created equally. For the purpose of this article, we will refer to the DualFlow 5K PSI. Qualified by DNV with an efficiency rating of 99.8% for topside separation down to 20 microns and up to 10,000 microns. The DualFlow 5K PSI is a market leader in solids management and is particularly adept at multiphase solids separation. This means they are designed for optimizing production on both gas and oil producing wells and, at the same time, handling the solids in return with high efficiency.
There are many differentiators between regular desanders and smart desanders; this article aims to outline the key differentiators from a design and engineering perspective.
1. Two cyclonic desanders in one unit
The unique design of the DualFlow 5K PSI means that there are two cyclones in the system as standard. This provides the user with options on how to achieve their desired goals. The desander’s cyclones can be operated in parallel or serial mode. Each position brings about its own benefits:
• The parallel position can be used when there is a higher flow rate, it can split the flow and lower the differential pressure over the system.
• The serial position provides double separation. The production goes through both cyclones as they are lined up behind each other. It is ideal for low flow, and low differential pressure.
The purpose-built design of the DualFlow means that it is possible to change positions while an operation is underway, offering the best of both situations. It is normal to start a well in serial and then move to parallel if the well has a high flow rate. This is done without any interruption to production, meaning the design, with two desanders in one unit, provides a high level of flexibility for an operation.
An additional benefit of two cyclones is contingency is built in as standard. If one is bypassed for a flushing sequence to empty solids, the other continues to operate.
• The parallel position can be used when there is a higher flow rate, it can split the flow and lower the differential pressure over the system.
• The serial position provides double separation. The production goes through both cyclones as they are lined up behind each other. It is ideal for low flow, and low differential pressure.
The purpose-built design of the DualFlow means that it is possible to change positions while an operation is underway, offering the best of both situations. It is normal to start a well in serial and then move to parallel if the well has a high flow rate. This is done without any interruption to production, meaning the design, with two desanders in one unit, provides a high level of flexibility for an operation.
An additional benefit of two cyclones is contingency is built in as standard. If one is bypassed for a flushing sequence to empty solids, the other continues to operate.
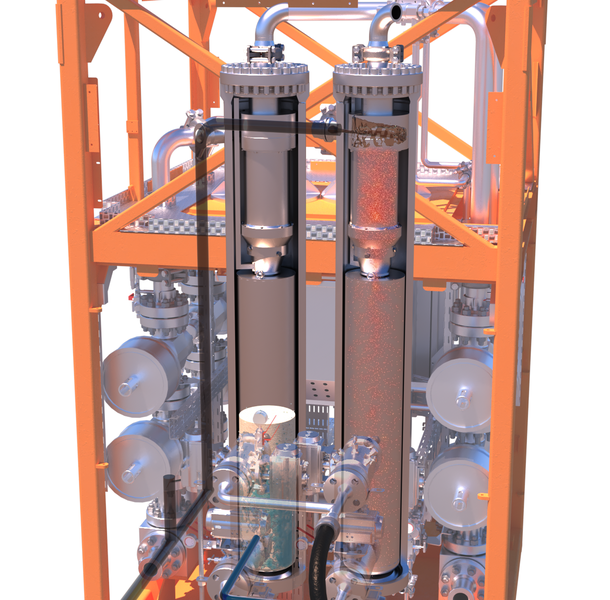
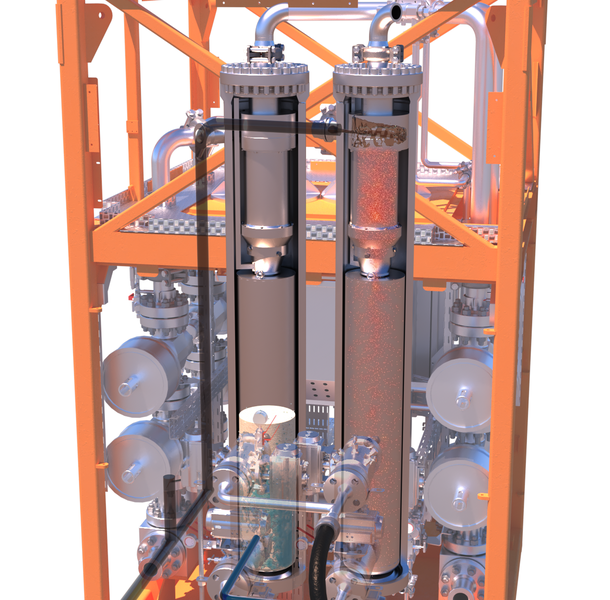
2. Big single liners
In the cyclone itself, the DualFlow has one big single liner as part of its design. This is markedly different from other desanders that have multi-liners or no liners. The big single liners are designed to optimise production while handling solids at a high efficiency rate. It has also been designed to separate a broad range of particle sizes (20 – 10 000 micron) and is designed to be geometrically advanced to achieve this.
In comparison, multi-liners were originally intended to separate oil from water. Therefore, with a multi-liner, it’s hard to remove solids from the liner once they enter the unit. This causes the solids to rip the liner and reduces efficiency. However, on cyclones with no liners inside the vessel, the force can drag solids out of the bucket, reducing separation efficiency.
In comparison, multi-liners were originally intended to separate oil from water. Therefore, with a multi-liner, it’s hard to remove solids from the liner once they enter the unit. This causes the solids to rip the liner and reduces efficiency. However, on cyclones with no liners inside the vessel, the force can drag solids out of the bucket, reducing separation efficiency.
3. Large sensor package
The true benefit of the sensors is that the customer will know when solids are expected, as well as the volume. With close to 600 sensors built in, relevant data points are monitored with real-time data providing an accurate system-health picture. The live ‘weight readings’ are a patented feature of the DualFlow and allow operators to learn how the well behaves while identifying and recognising trends concerning sand production from the well. Working together with the customer, the solids experts can manage the system to respond to changes made to optimise oil and gas production and enhance the well’s lifecycle.
4. Sophisticated control system and Human Machine Interface (HMI)
The DualFlow has a sophisticated control system with quality components. It reduces the complexity and downtime of the system. It also makes troubleshooting much easier thanks to its user-friendly interface. As the control system can be operated remotely using the HMI it means POB is directly reduced. The HMI is the touchscreen and dashboard that allows the user to communicate with the DualFlow. The HMI provides the same information whether the operator is located offshore or onshore in the FourPhase Operations & Technology Center in Bergen.
Flexibility is further boosted with the DualFlow via the control system. If a project is experiencing a higher flow rate and needs to bolster its separation ability, an extra DualFlow or other auxiliary systems can easily be added to the control system via an Over The Air (OTA) update without the need for additional POB.
The DualFlow system does not feature any manual valves on the system. This increases the safety perspective of the equipment and removes a time-consuming mundane task. As all the valves are interlocked, it means that no valve can be opened incorrectly and removes the issue of human error – directly preventing hydrocarbons from going where they are not supposed. A key benefit is that operators can be kept focused on what they are supposed to be doing – production optimisation. The sensors also predict when maintenance will be due, directly preventing wear and tear. Its remote ability directly leads onto the system’s remote monitoring capabilities.
Flexibility is further boosted with the DualFlow via the control system. If a project is experiencing a higher flow rate and needs to bolster its separation ability, an extra DualFlow or other auxiliary systems can easily be added to the control system via an Over The Air (OTA) update without the need for additional POB.
The DualFlow system does not feature any manual valves on the system. This increases the safety perspective of the equipment and removes a time-consuming mundane task. As all the valves are interlocked, it means that no valve can be opened incorrectly and removes the issue of human error – directly preventing hydrocarbons from going where they are not supposed. A key benefit is that operators can be kept focused on what they are supposed to be doing – production optimisation. The sensors also predict when maintenance will be due, directly preventing wear and tear. Its remote ability directly leads onto the system’s remote monitoring capabilities.
5. Compact footprint
The technology is the only dual cyclone desander on the market with a 2x2 meter footprint. The smallest desander available, its modular design was strategically developed to create a flexible, stackable and compact solution. The small size enables it to be lowered through the hatch deck and be kept away from the often busy rig floor. The technology weighs less than 10t and requires minimal logistical impact. Operationally supported by integrating 3D modelling and visualisations in the project planning phase, rig-ups are performed virtually enabling specific elements to be detailed ahead of mobilisation, saving valuable hours offshore. The technology is stackable with auxiliary equipment such as choke manifolds and filter units.
In our next article, we will discuss how these clever design features deliver a large amount of operational and logistical benefits to a project. Major benefits include increased ESG metrics, enhanced safety and cost control features.
In our next article, we will discuss how these clever design features deliver a large amount of operational and logistical benefits to a project. Major benefits include increased ESG metrics, enhanced safety and cost control features.